Navigating Industry 4.0 through Legacy Equipment: A Practical Strategy
Modernizing existing manufacturing facilities doesn't necessitate scrapping equipment or making hefty capital investments in shiny new smart factories. Rather, strategic integration of digital capabilities into legacy systems can lead to remarkable improvements without breaking the bank.
Take, for instance, a Midwestern automotive components plant filled with machinery dating back to the 1980s. The operations manager there, like many others in similar situations, acknowledged the lack of connectivity among their machines but didn't see a reason to discard them. This sentiment aligns with research on sustainable manufacturing practices from Deloitte, making perfect sense from both an economical and environmental standpoint.
So, how do we bridge this gap between outdated infrastructure and the promise of Industry 4.0?
According to a study from the Manufacturing Leadership Council, over 70% of manufacturing equipment in North America is decades old. With billions invested in this capital and years of embedded process knowledge, the answer lies in finding ways to make these old dogs new tricks through digital transformation.
Strategies for Integrating Legacy Equipment:
1. Sensor retrofitting: the digital nervous system
The first step to any digital transformation is gathering data. Modern IoT sensors can be seamlessly added to machinery without significant modifications, sensing conditions like vibration, temperature, and energy consumption. For example, a precision metal components manufacturer installed wireless vibration sensors on 1990s-era CNC machines for under $500 per machine, enabling them to detect wear patterns and move from reactive maintenance to a predictive approach, reducing unplanned downtime by an impressive 37%.
2. Edge computing: intelligence at the source
Small, industrial-strength computers can be installed near equipment to collect, process, and act on data. Take a paper products manufacturer that added compact edge computers to its converting lines, allowing them to analyze subtle variations in product weight in real-time. The system could detect drift conditions and automatically adjust machine parameters, resulting in a 8.2% reduction in material waste without needing to replace any core equipment. Plus, edge computing enables facilities to begin their digital journey without waiting for comprehensive IT infrastructure upgrades.
3. Middleware solutions: building digital bridges
Modern middleware platforms created for manufacturing environments can extract data from legacy protocols and translate it into contemporary formats. A food processing company leveraged such middleware to connect 1990s-era PLCs with their modern MES system, investing in software to communicate across these technological generations instead of replacing functional equipment. The result was a unified digital thread offering real-time visibility across their entire operation, all while costing approximately 15% of what equipment replacement would have.
Identifying High-Value Retrofit Opportunities:
Not every piece of legacy equipment requires equal attention when it comes to digital capabilities. Prioritization demands a structured approach, centered on three key dimensions: critical path analysis, data value assessment, and ROI-driven implementation.
Take, for instance, a medical device manufacturer struggling with inconsistent throughput. Critical path analysis revealed it was their assembly systems, rather than the aging molding machines, that limited production. By digitizing the assembly equipment first, they achieved a 23% improvement in throughput with minimal capital investment.
In conclusion, true digital transformation doesn't require starting from scratch. By thoughtfully integrating digital solutions, prioritizing development based on specific needs, and following a phased roadmap, manufacturers can transform their operations one enhancement at a time, ultimately delivering the benefits of Industry 4.0 while safeguarding existing investments WEF.
- To gather data for digital transformation, modern IoT sensors can be retrofitted onto machinery without significant modifications, measuring conditions such as vibration, temperature, and energy consumption, as demonstrated by a precision metal components manufacturer.
- Edge computing, which involves installing small, industrial-strength computers near equipment to collect, process, and act on data, can enable facilities to analyze real-time conditions and make adjustments without replacing core equipment, as shown by a paper products manufacturer.
- Middleware solutions designed for manufacturing environments can translate data from legacy protocols into contemporary formats, connecting older systems with modern software, like the food processing company that used middleware to connect 1990s-era PLCs with their MES system.
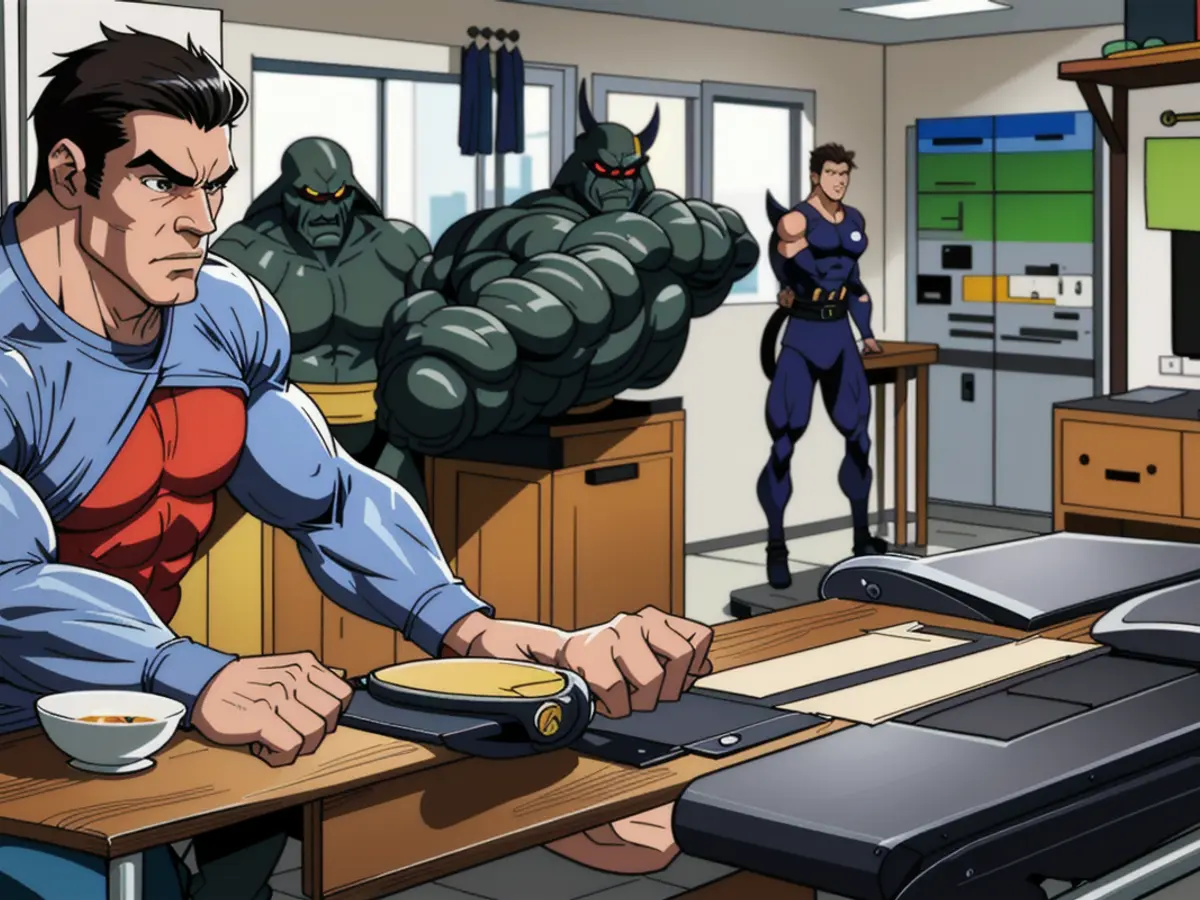
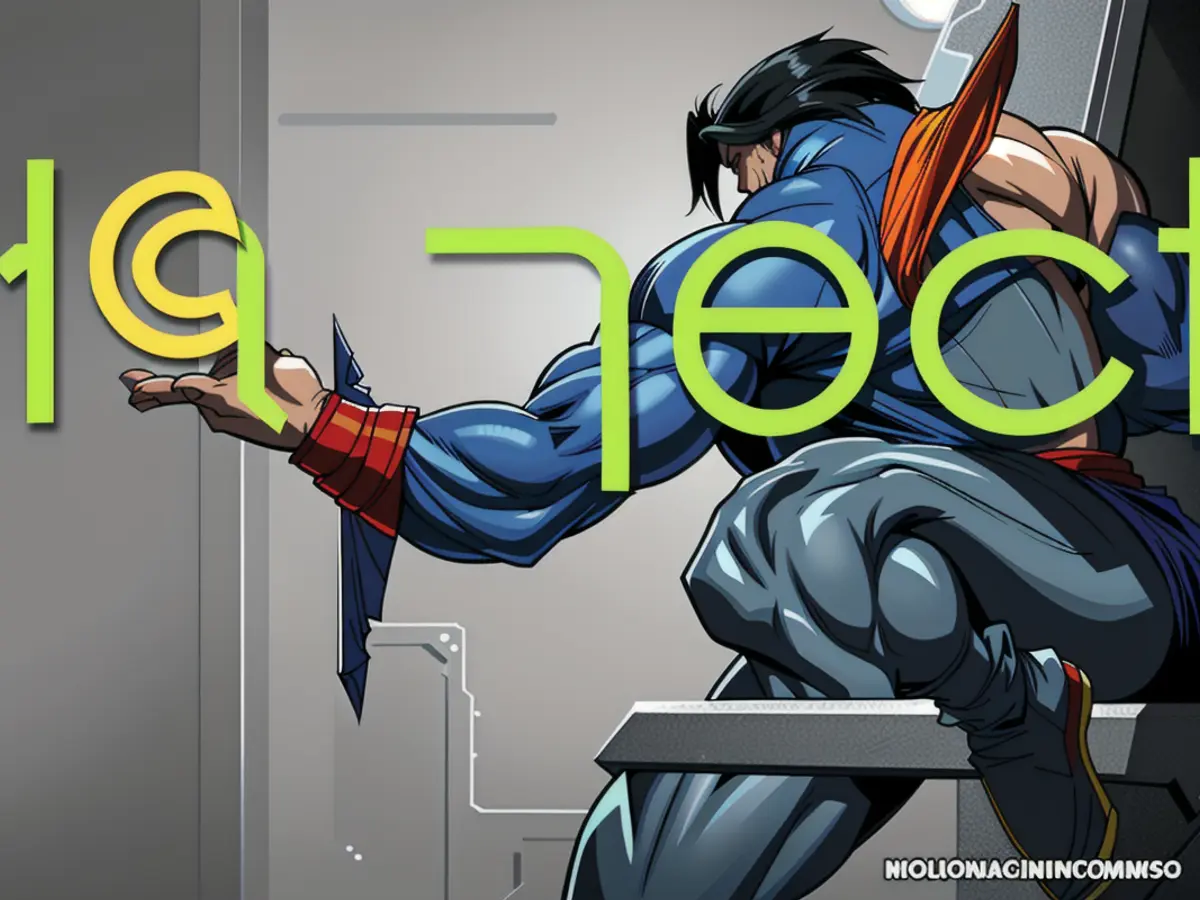
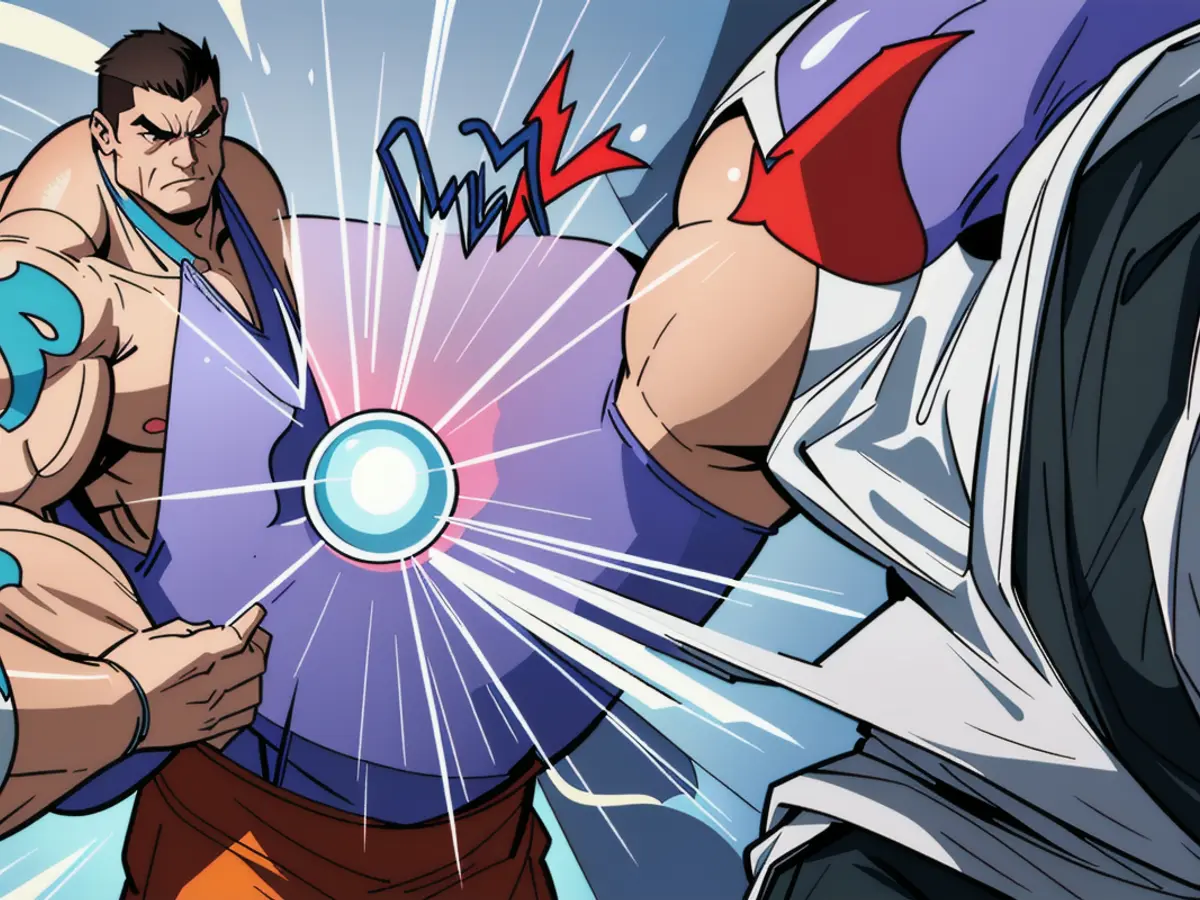
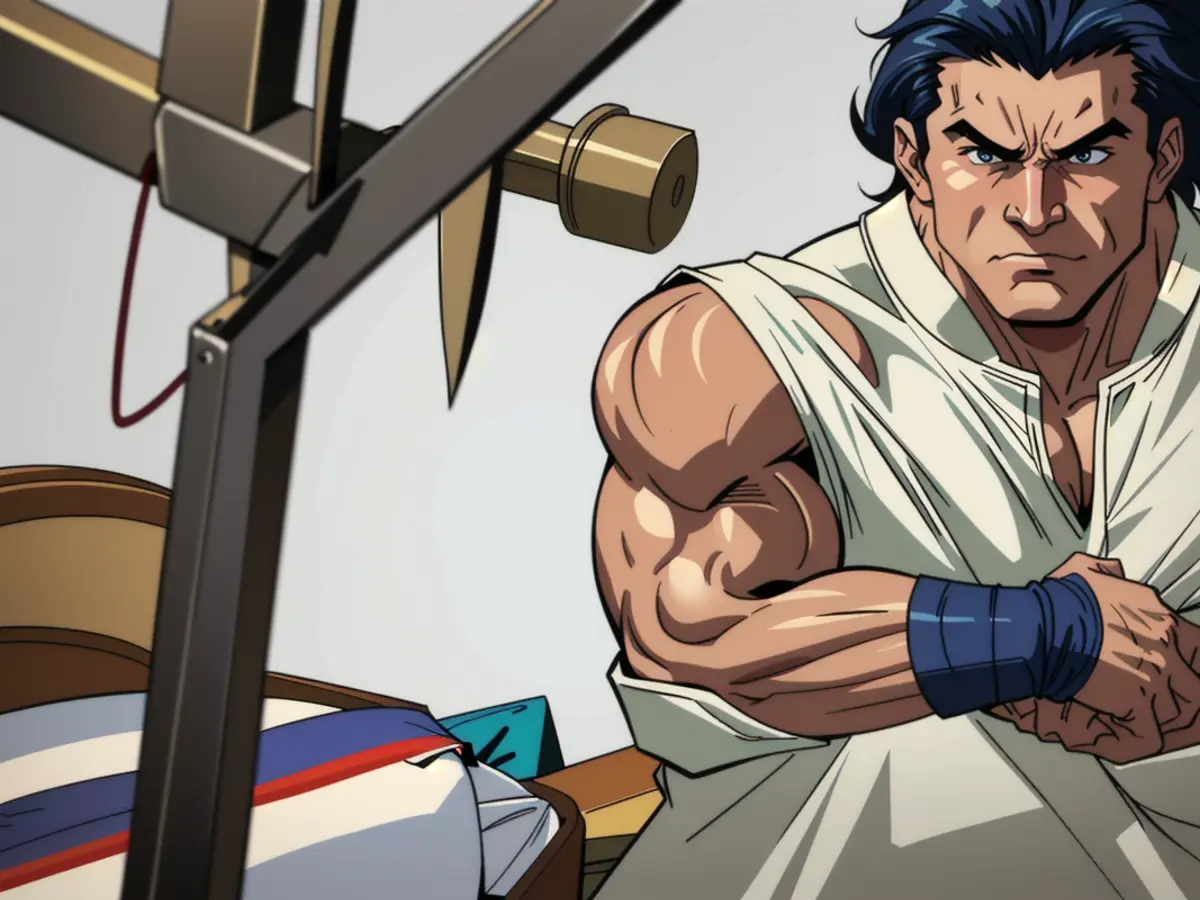
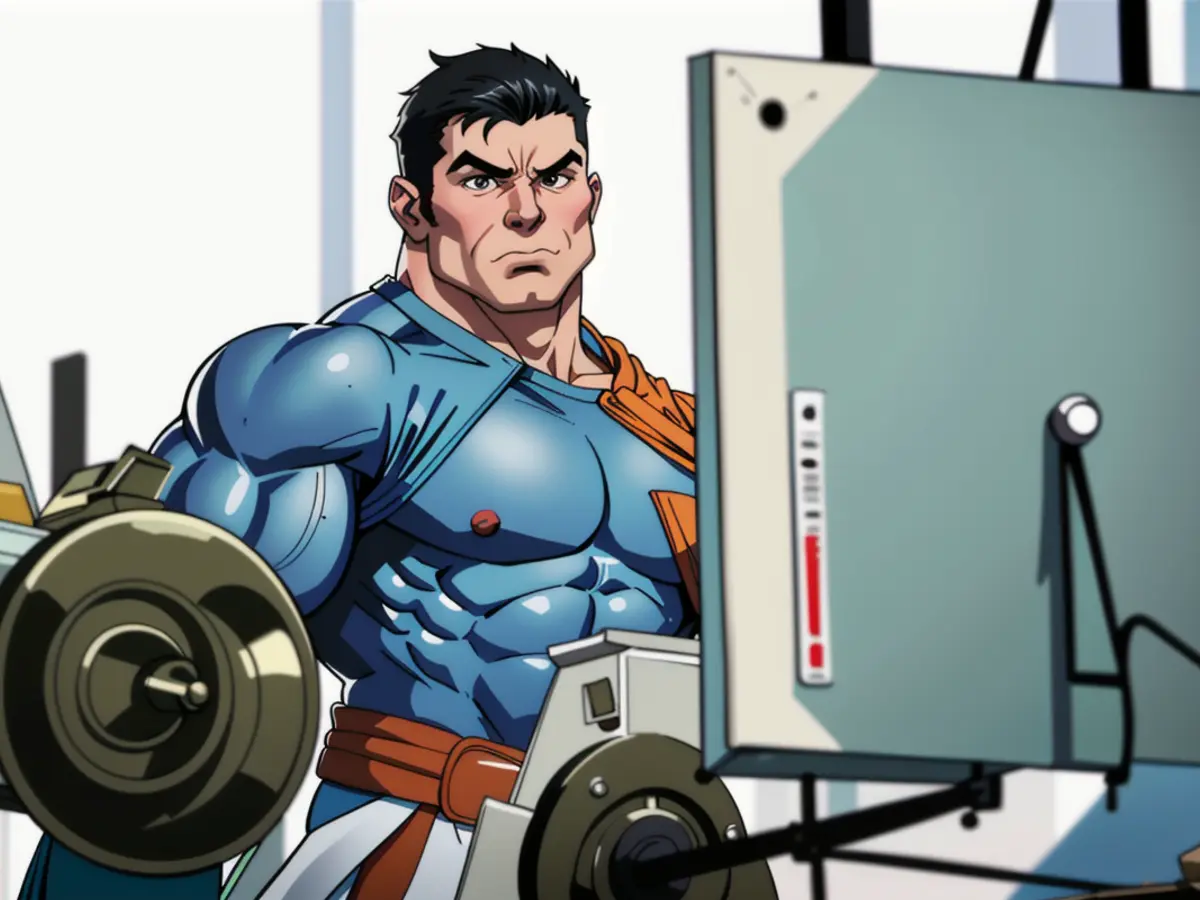
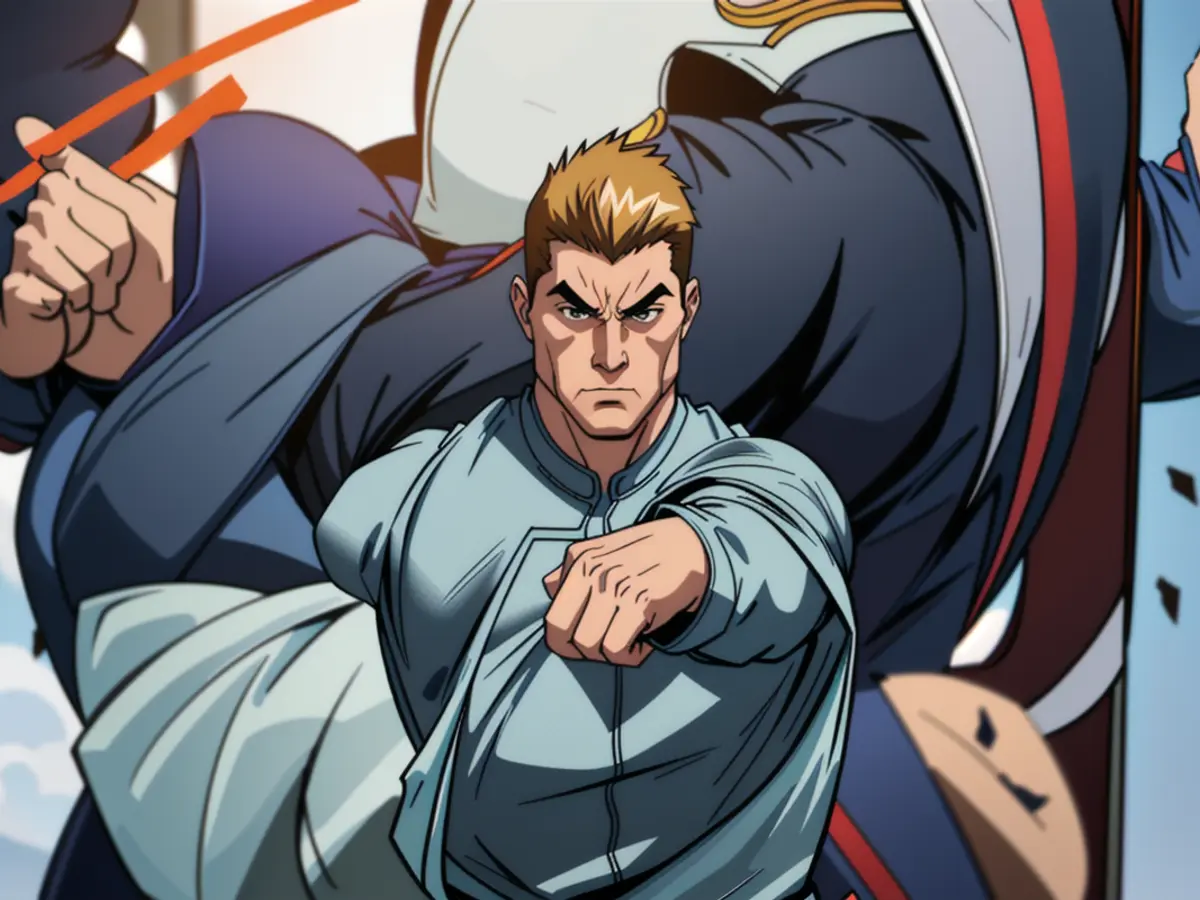
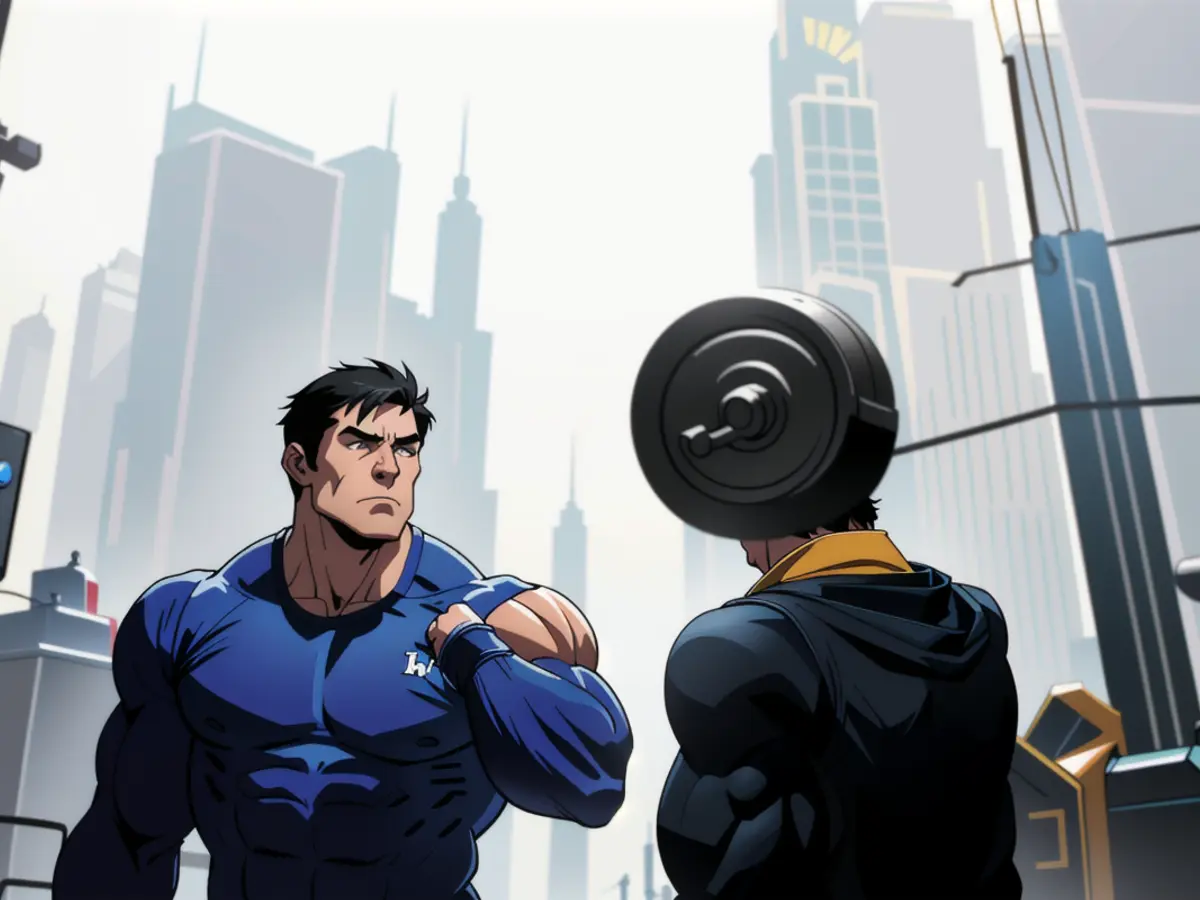
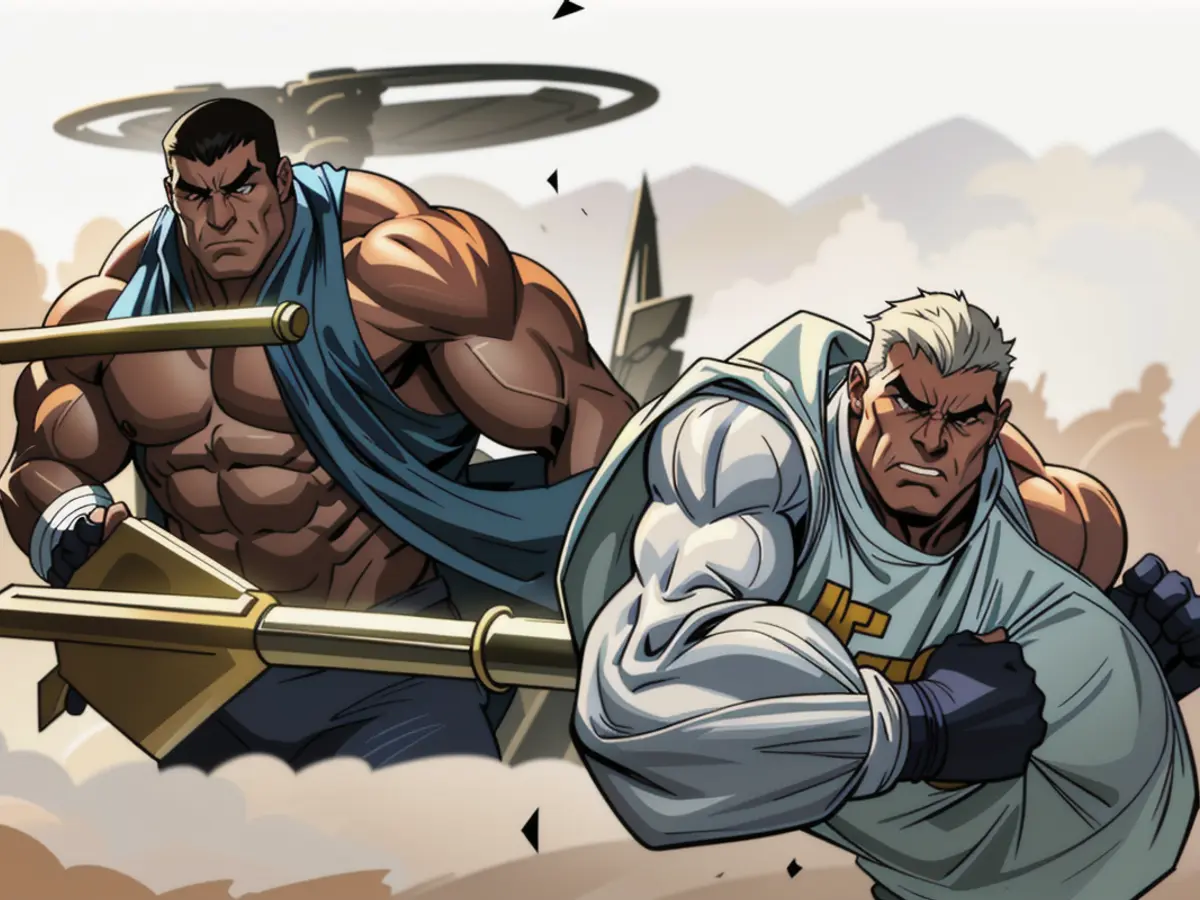
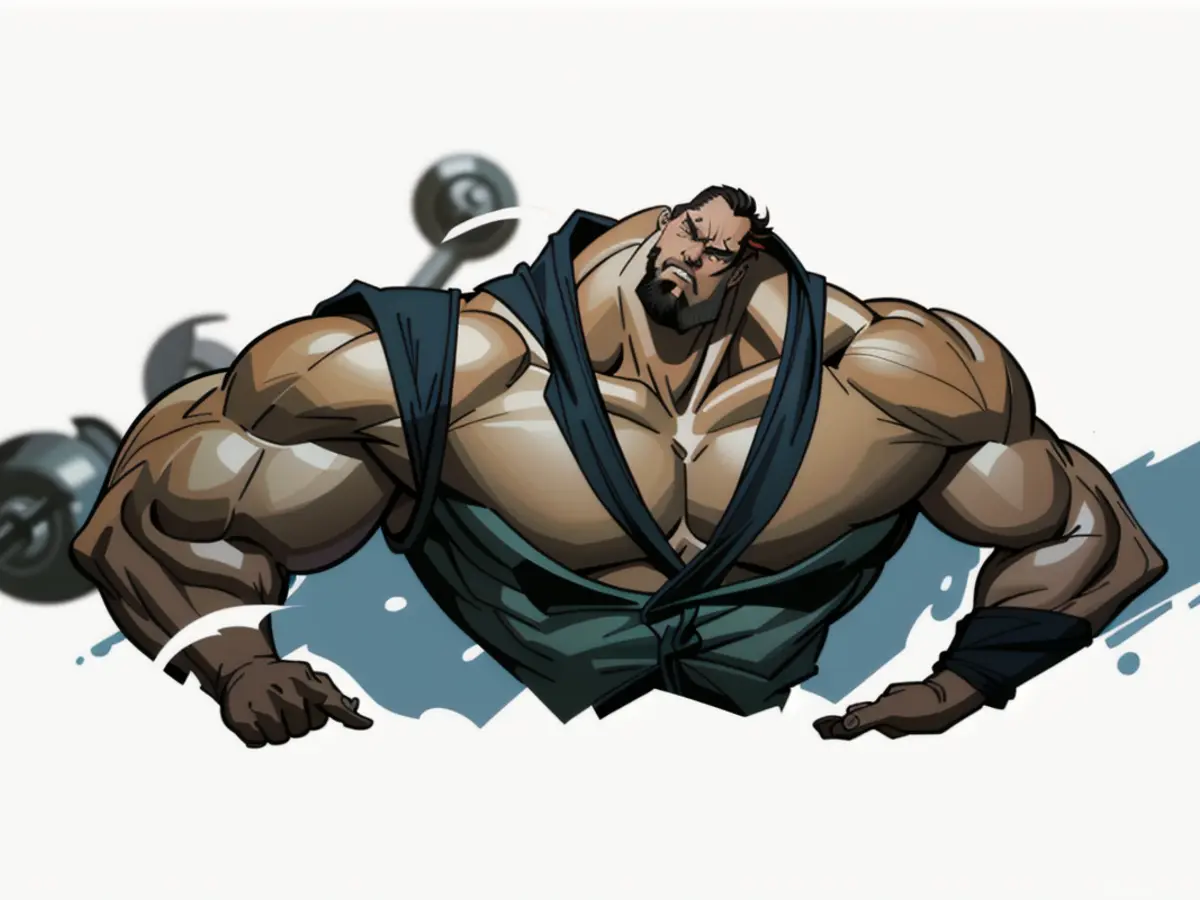
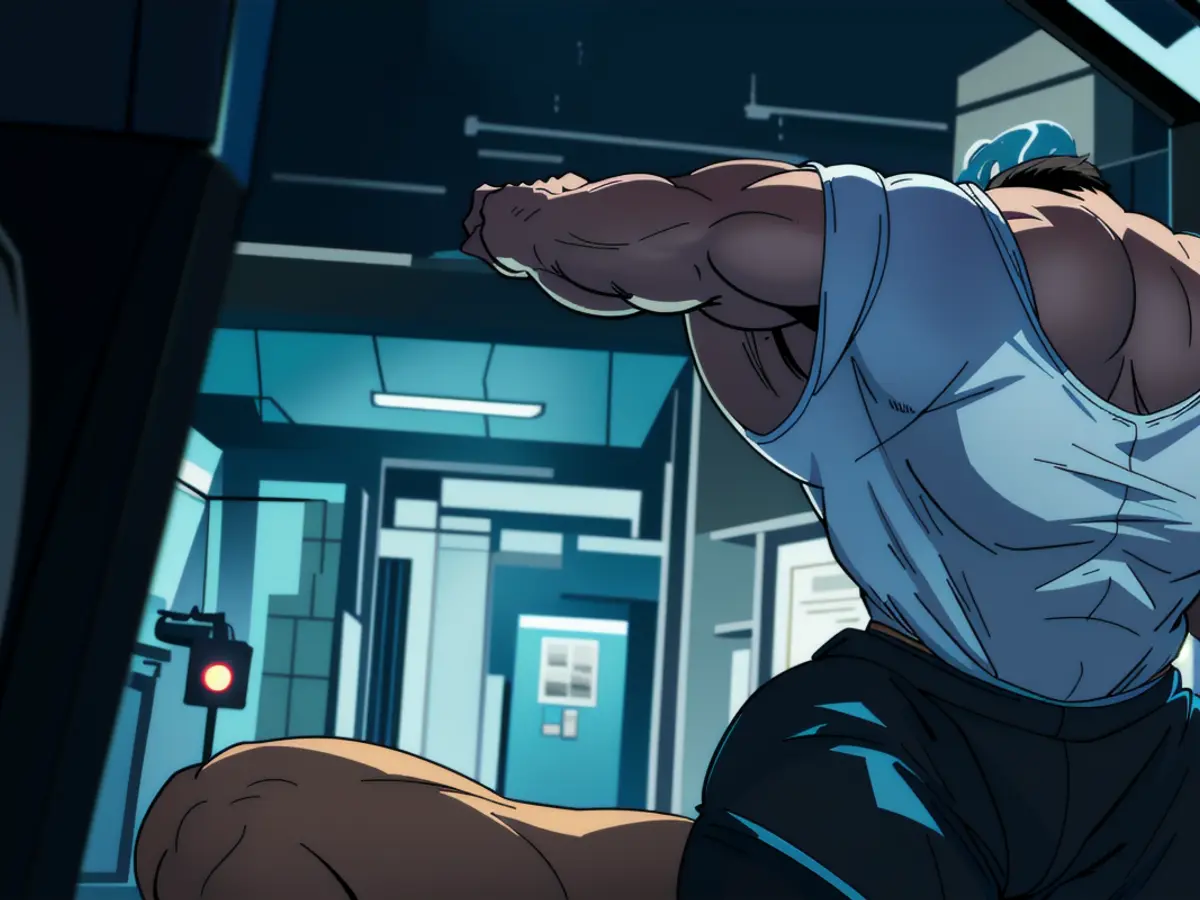
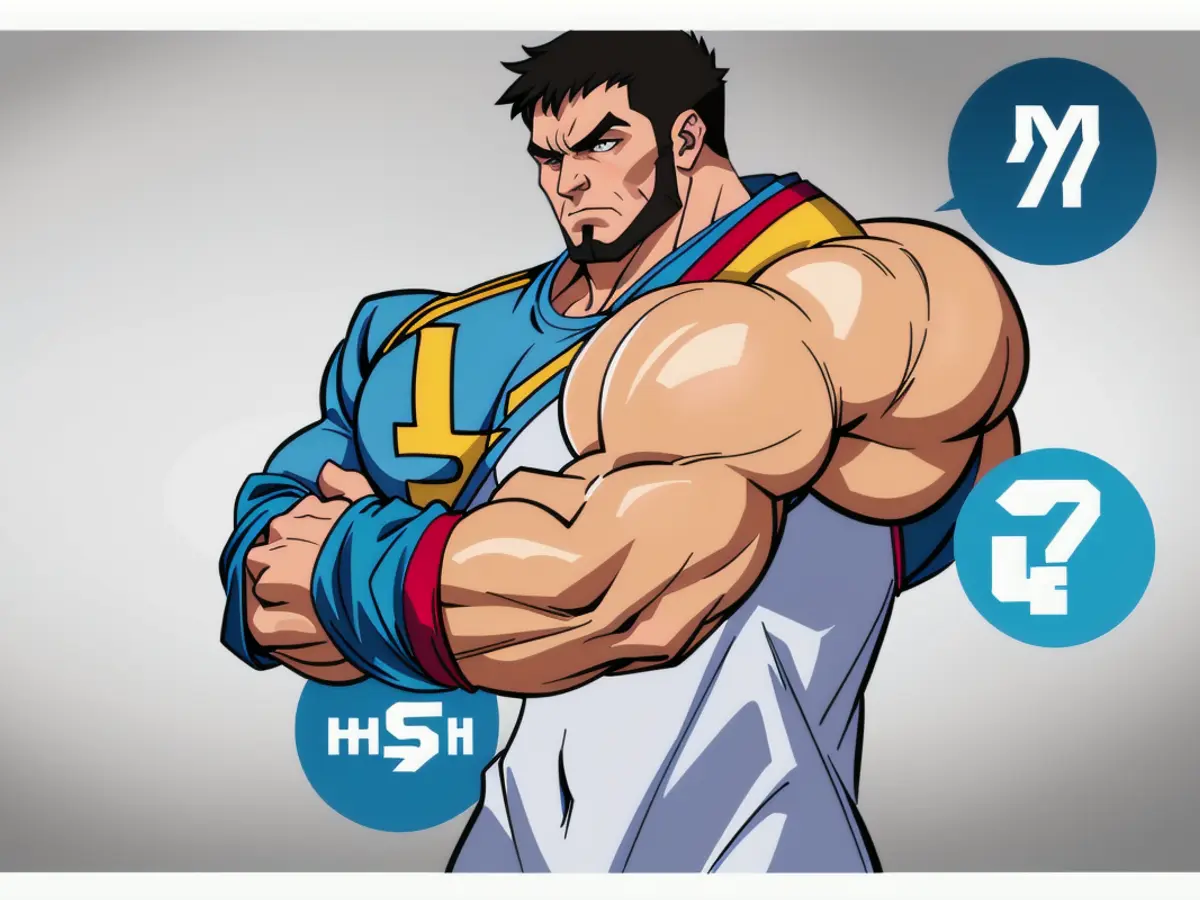
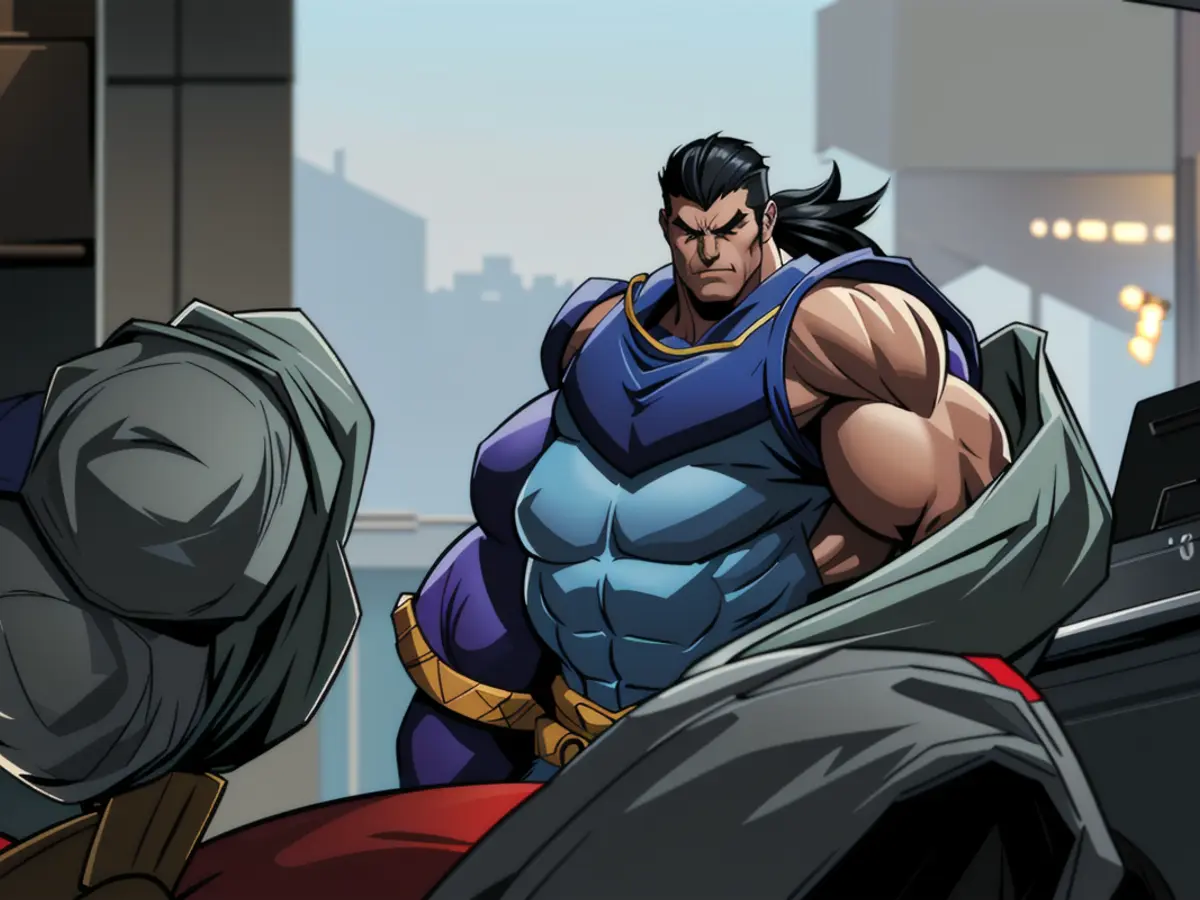
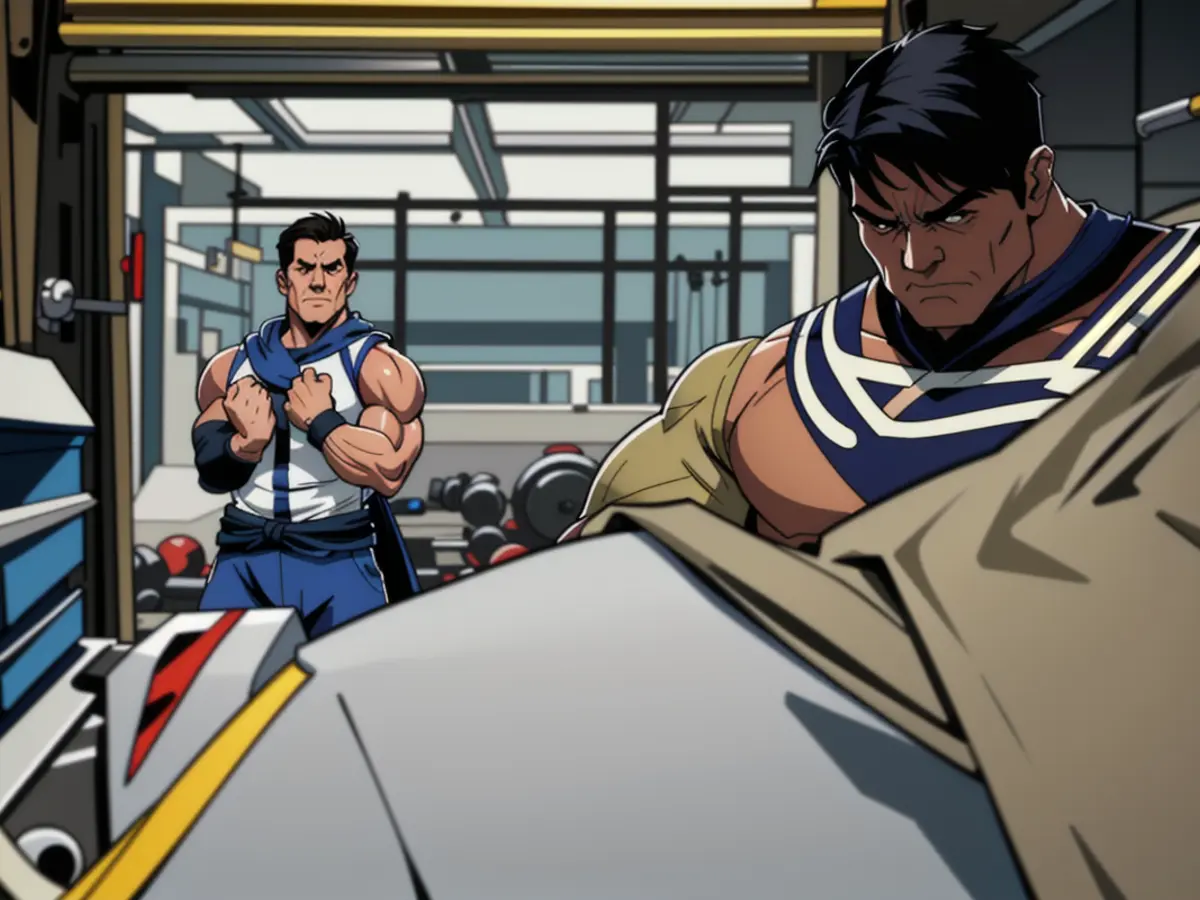
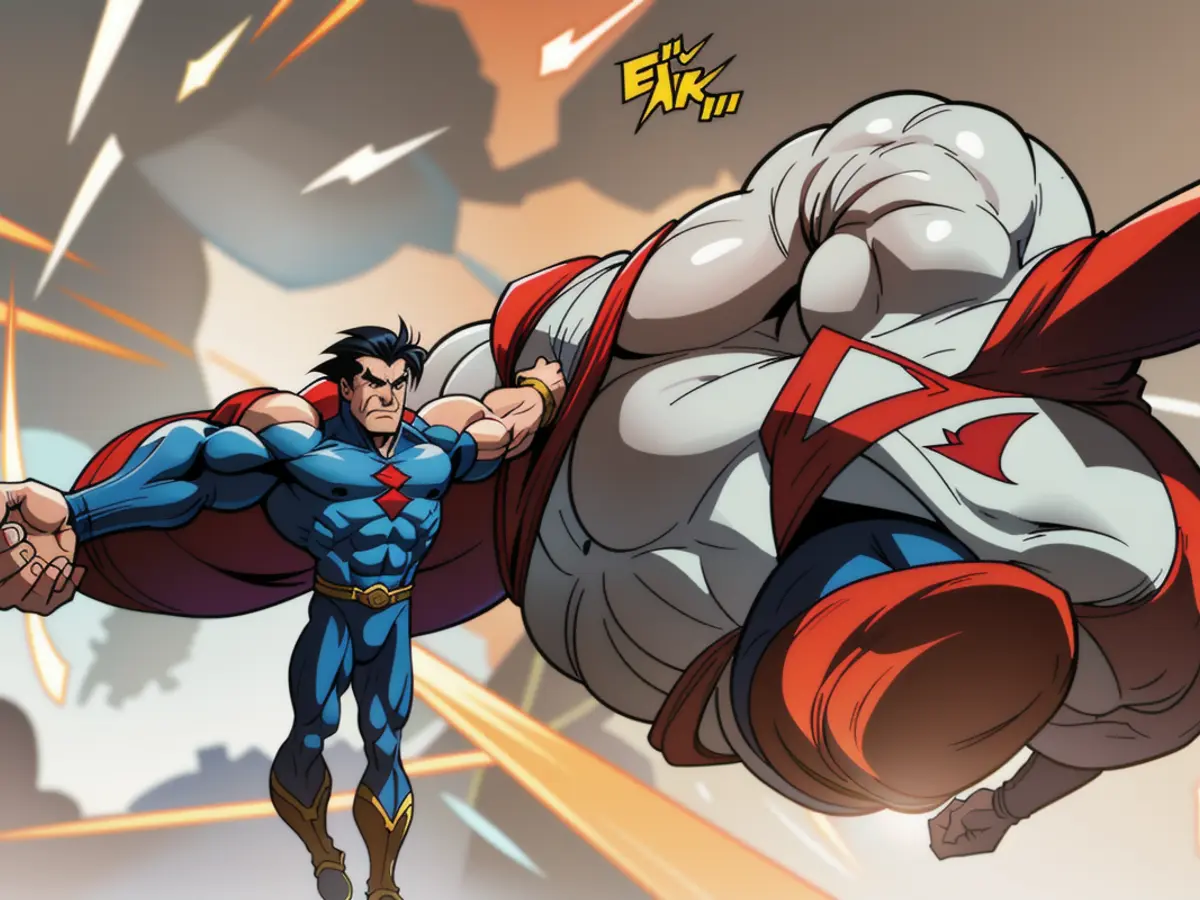
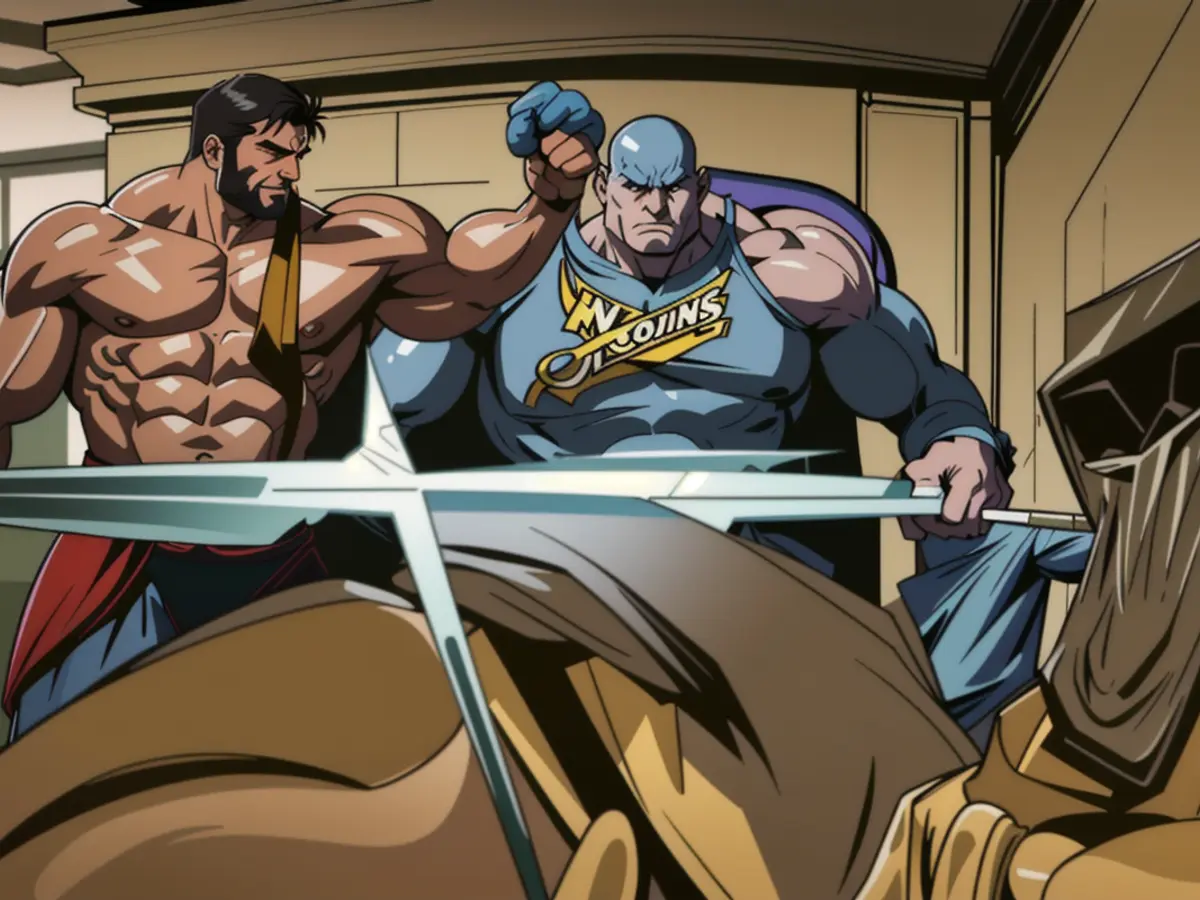
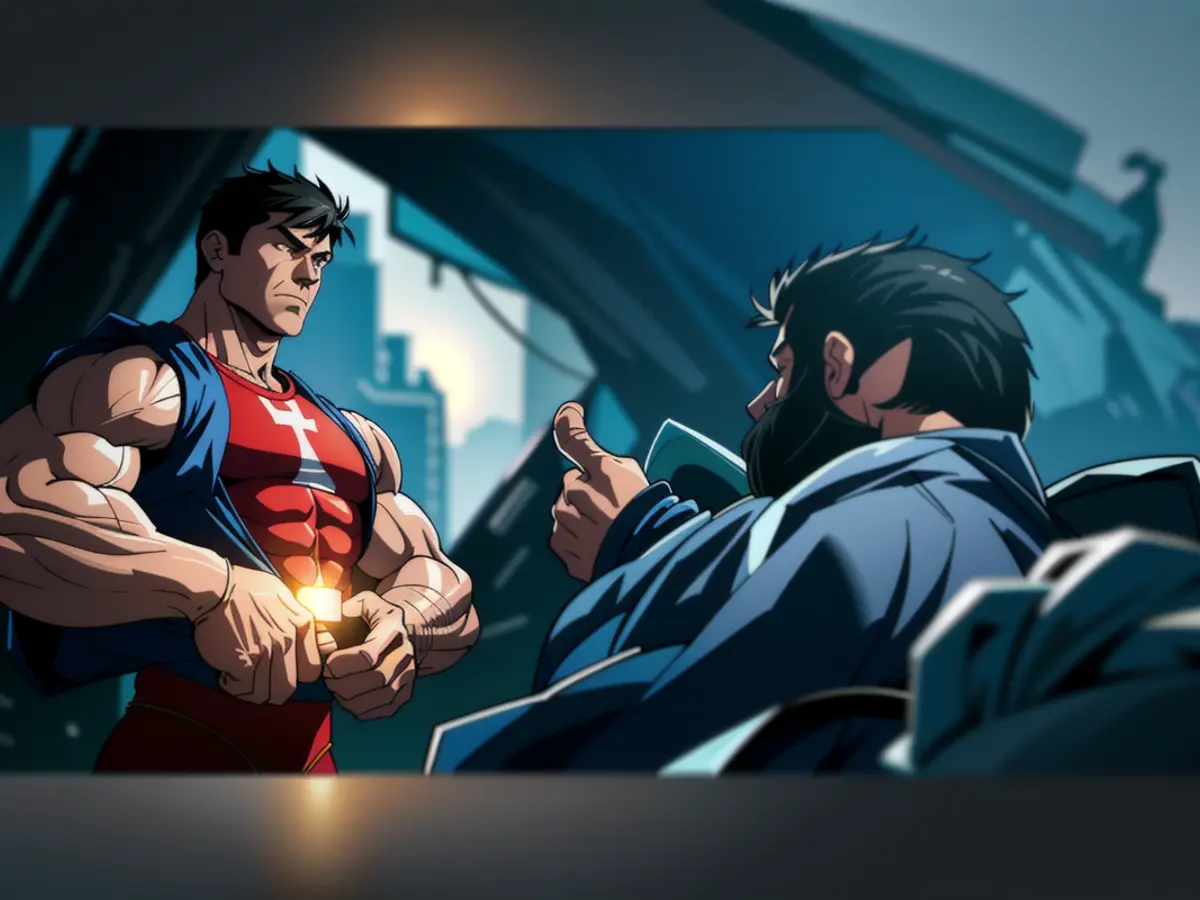
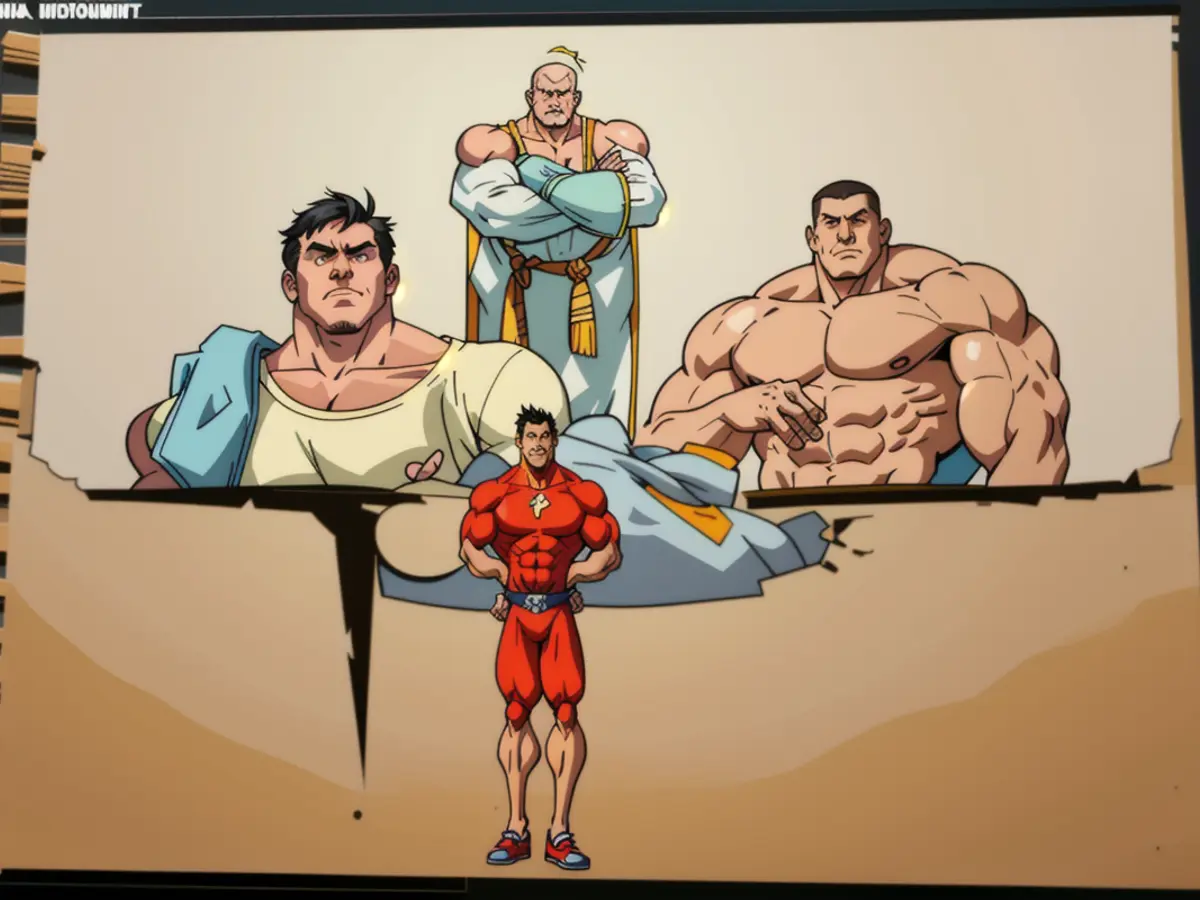
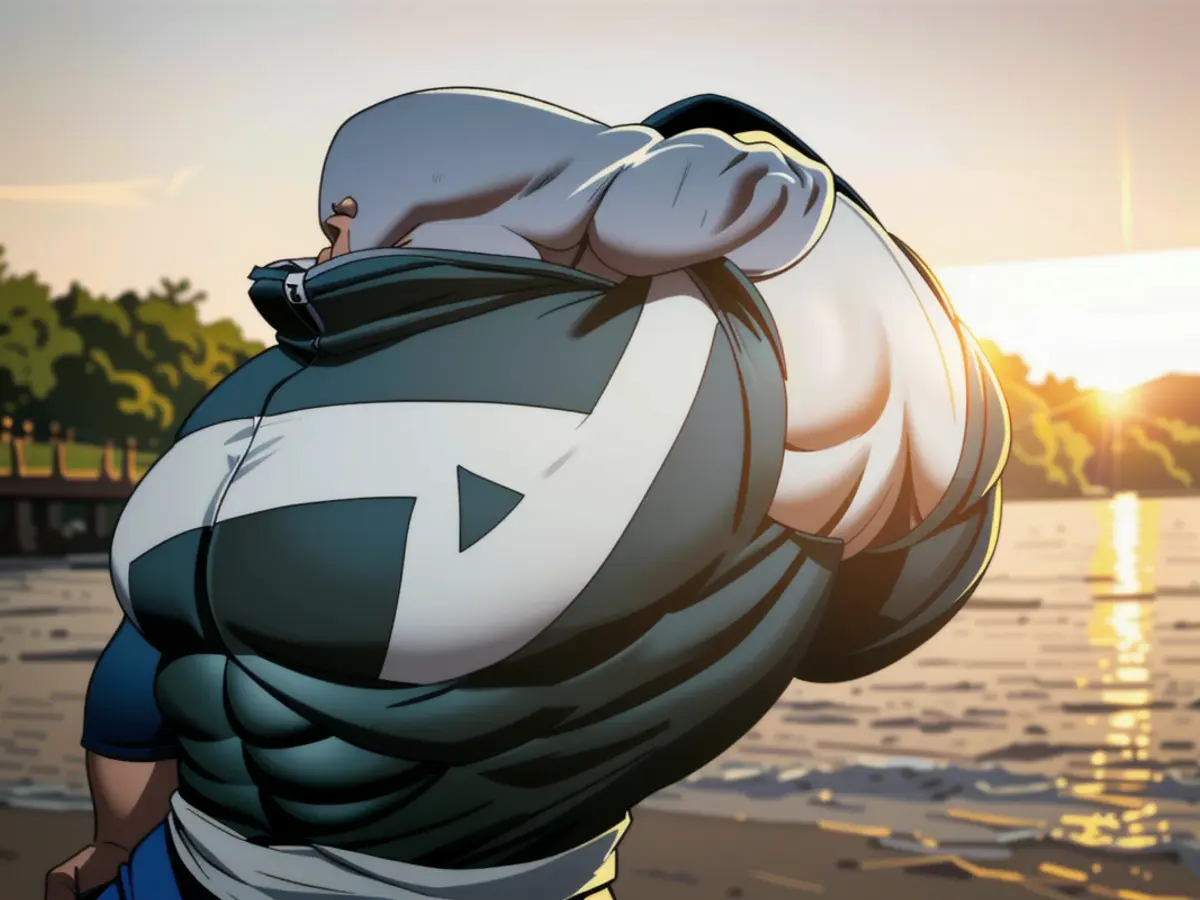
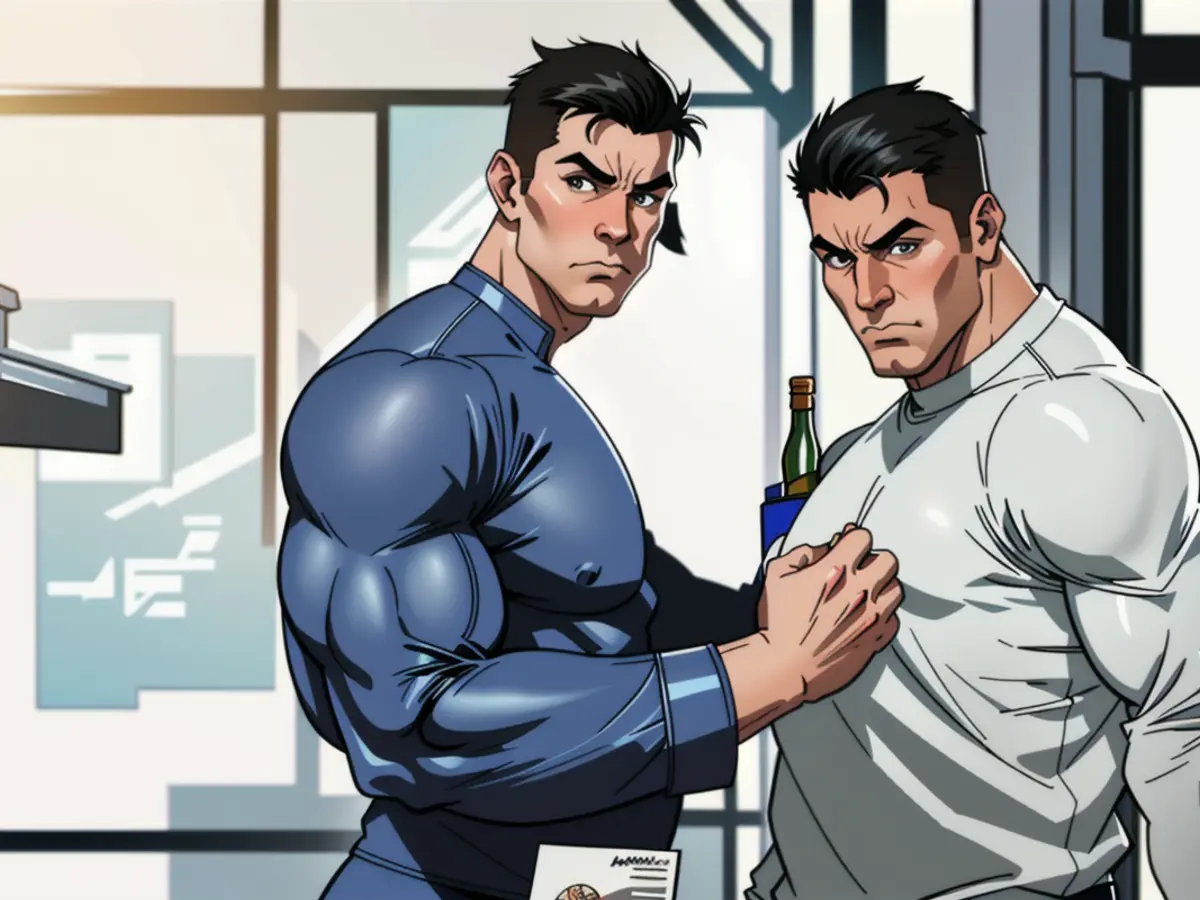
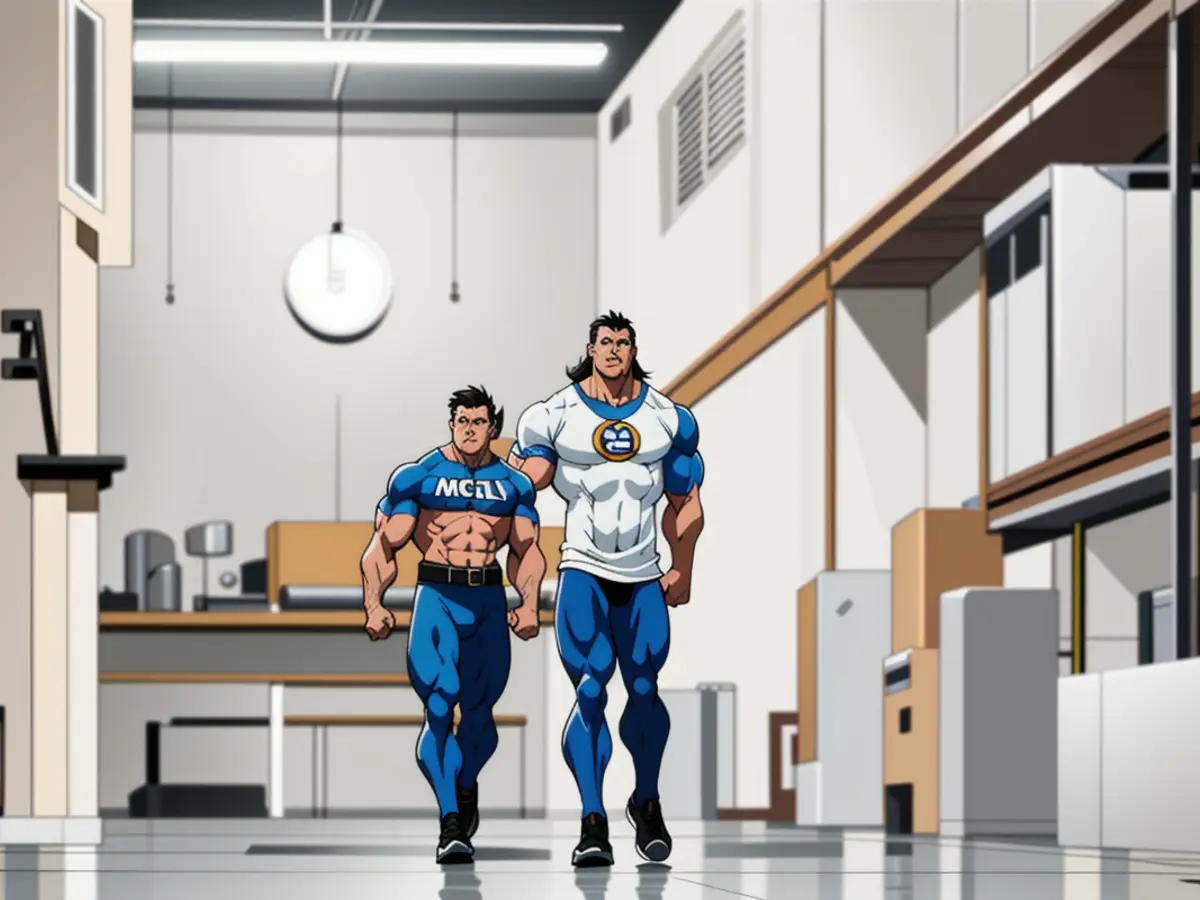